Key Advantages and Factors To Consider of Implementing Plastic Extrusion in Your Projects
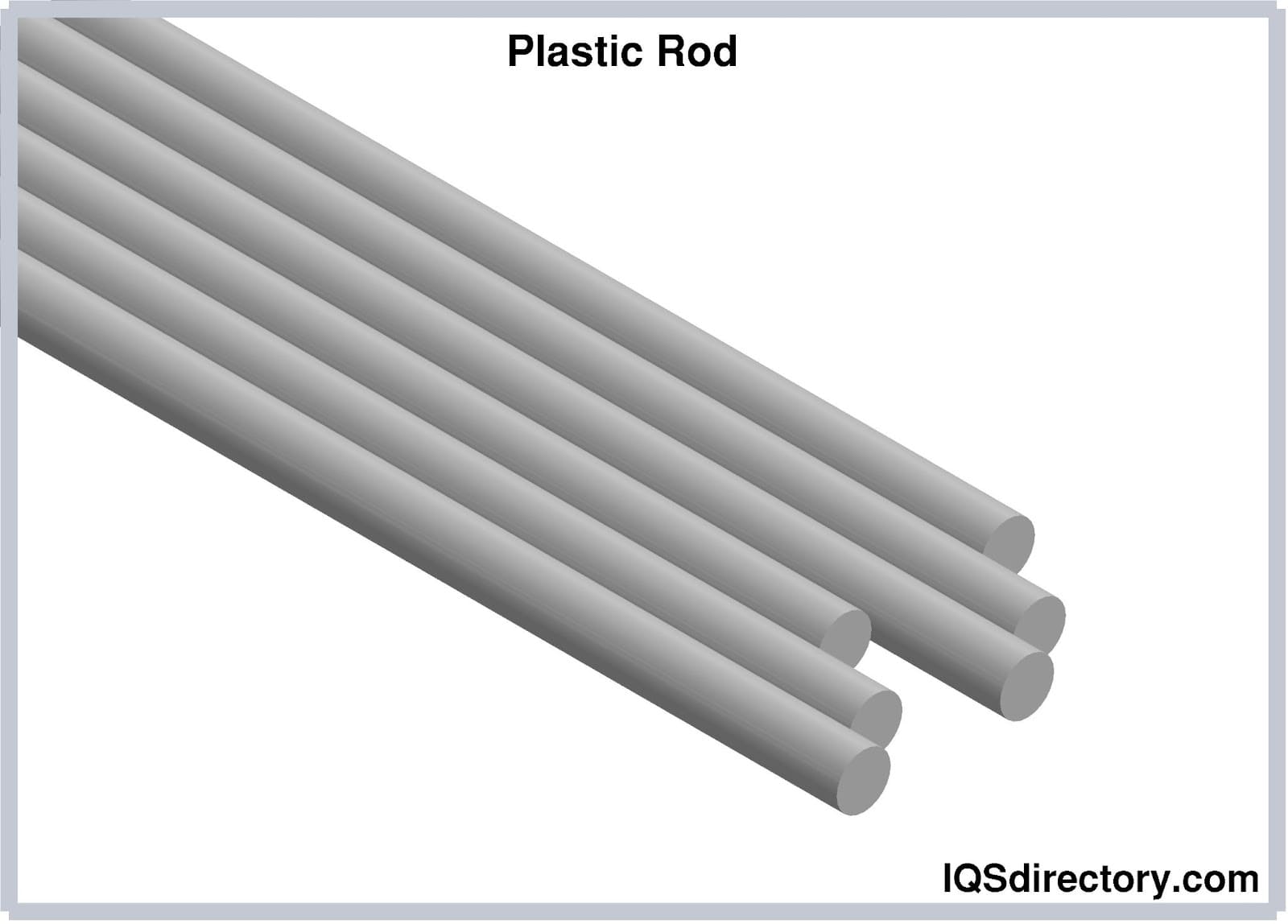
Understanding the Fundamentals of Plastic Extrusion
Plastic extrusion, a staple in the production sector, is a procedure that involves melting raw plastic product and improving it into a continual account. The elegance of plastic extrusion exists in its adaptability. The selection of plastic and the style of the die identify the product's qualities.

The Economic Benefit of Plastic Extrusion
The economic advantage of plastic extrusion lies primarily in 2 areas: affordable material manufacturing and beneficial production rates. With plastic extrusion, companies can generate high volumes of product at a lower cost compared to various other approaches. The procedure boasts a remarkable production speed, considerably reducing time and additional boosting its financial stability.
Economical Material Production
A considerable benefit of plastic extrusion is its amazing cost-effectiveness. Furthermore, the extrusion procedure allows for a high level of accuracy in forming the plastic, minimizing the need for costly post-production changes or corrections. All these aspects make plastic extrusion a highly affordable selection for many jobs, supplying an attractive balance in between expense and performance.
Beneficial Manufacturing Speeds
While keeping the cost-effectiveness of the products, another notable advantage of plastic extrusion lies in its rapid production speeds. This mix of high quality, rate, and cost-effectiveness highlights the considerable economic advantage of applying plastic extrusion in different projects.
Versatility and Customization: The Staminas of Plastic Extrusion
Among the prominent toughness of plastic extrusion lies in its adaptability and modification capacity. These high qualities open the door to limitless design opportunities, offering manufacturers the capability to customize products to specific demands. This increased degree of modification not just boosts product capability however likewise considerably improves item individuality.
Unrestricted Style Opportunities
Plastic extrusion radiates in its capability to use virtually infinite layout opportunities. This approach offers flexibility to create elaborate accounts and complex forms, a feat tough to achieve with various other construction methods. Owing to the fluid nature of liquified plastic, the process is versatile sufficient to generate a diverse series of sizes, forms, and measurements. The plastic can be controlled to match distinct specs, permitting the production of tailored geometries and conference particular customer needs. Plastic extrusion can deal with a selection of plastic kinds, broadening its application extent. This versatile strategy, consequently, offers a broad array of sectors from building click for info and construction to automotive, packaging to electronics, and past. With plastic extrusion, the design opportunities are essentially endless.
Boosting Product Uniqueness
The convenience of plastic extrusion can greatly boost item individuality. This procedure enables designers to experiment with various forms, sizes, and colors, giving them the flexibility to create special products that attract attention in the market. It is this customization that provides a distinct identification to every item, differentiating it from its rivals.
In addition to its visual benefits, the customizability of plastic extrusion also offers functional benefits. Thus, plastic extrusion not just enhances product uniqueness however also its utility and marketability.
Layout Limitations in Plastic Extrusion: What You Required to Know
Exactly how can design restrictions potentially impact the procedure of plastic extrusion? While plastic extrusion is functional, design limitations can curtail its advantages. Certain complicated styles may not be feasible because of the limitations of the extrusion process, potentially restricting the development of complex profiles. The process is much less ideal for multi-chambered or hollow frameworks. Furthermore, the extrusion procedure might not always supply the i thought about this desired surface coating, particularly for those needing high gloss or optical quality. Product choice can likewise position obstacles, as not all polymers appropriate for extrusion. High-temperature resistant plastics, as an example, may provide troubles. Recognizing these restrictions is crucial for reliable implementation of plastic extrusion in your projects. plastic extrusion.
Reviewing the Environmental Influence of Plastic Extrusion
While recognizing design constraints is a significant facet of plastic extrusion, it is just as essential to consider its ecological effects. The process of plastic extrusion includes melting plastic Look At This products, possibly releasing hazardous gases right into the atmosphere. Using recycled plastic materials in the extrusion process can lower environmental influence.
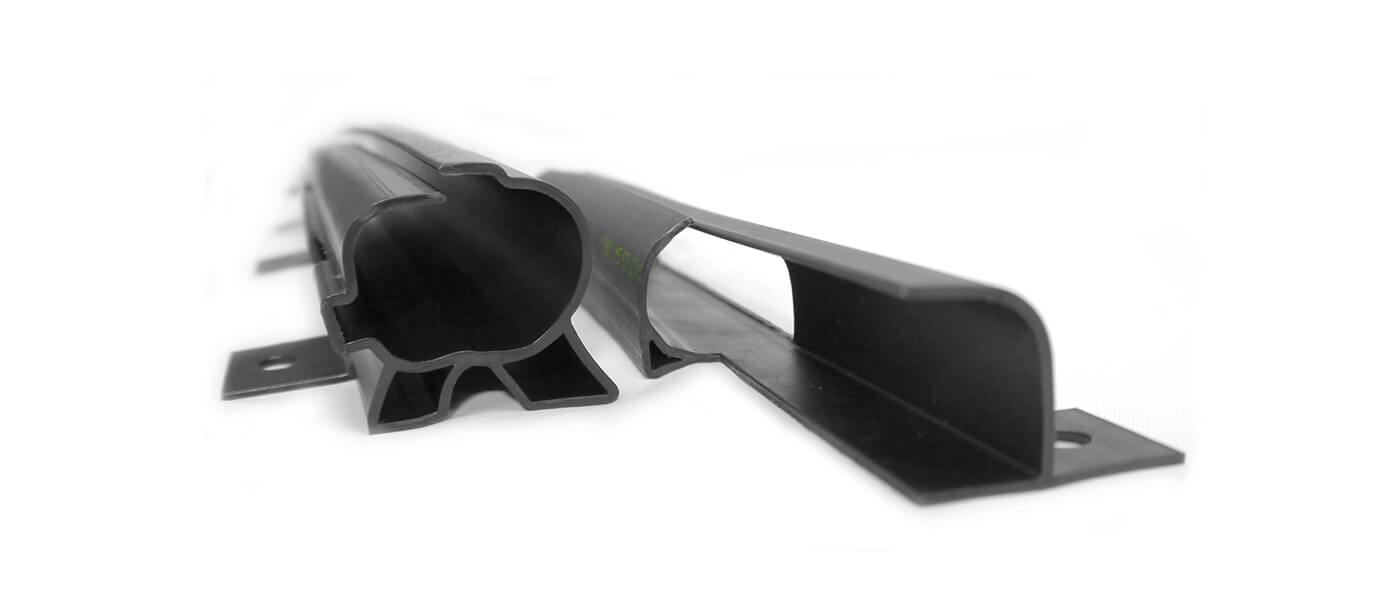
Situation Study: Effective Projects Utilizing Plastic Extrusion
Success tales in the field of plastic extrusion are plentiful, demonstrating both the versatility and effectiveness of this manufacturing process. plastic extrusion. An additional effective case is the manufacturing of plastic movie for product packaging and farming. These circumstances highlight plastic extrusion's critical duty in different industries, proving to its flexibility, cost-effectiveness, and reputable outcome.
Conclusion
In final thought, plastic extrusion supplies a effective and affordable technique for producing complex shapes with minimal waste. Incorporating plastic extrusion into projects can lead to successful end results, as confirmed by many instance researches.
Plastic extrusion, a staple in the manufacturing industry, is a process that involves melting raw plastic product and reshaping it right into a continuous profile. Plastic extrusion can deal with a range of plastic kinds, expanding its application range.Exactly how can make constraints potentially affect the procedure of plastic extrusion? The procedure of plastic extrusion includes melting plastic products, possibly releasing unsafe gases into the setting. Using recycled plastic materials in the extrusion procedure can reduce environmental influence.